The Real Deal - Developers are bracing themselves for the burn of Trump’s metal tariffs
Press - April 1, 2018
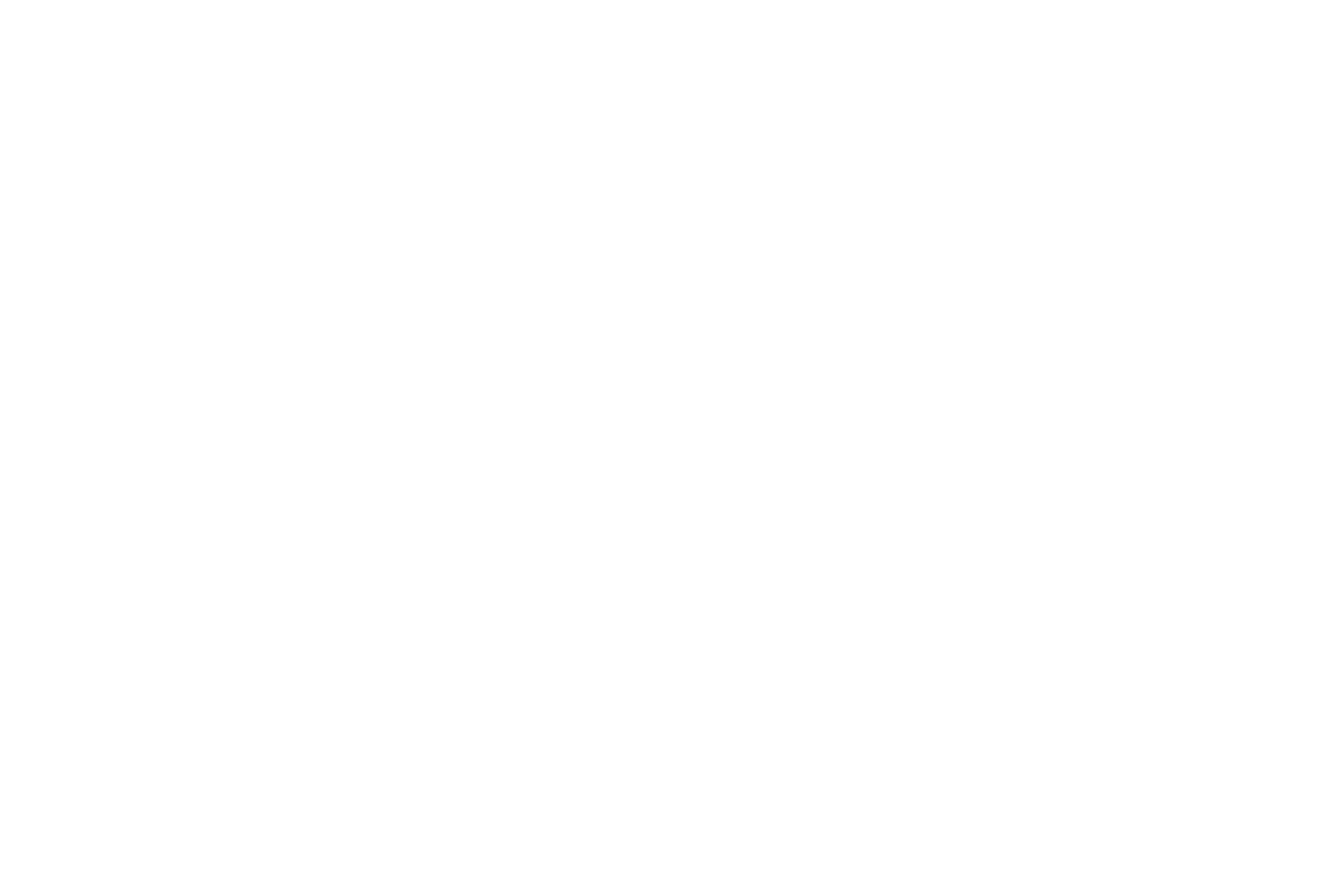
New York City developers and builders certainly won’t strike gold with the Trump administration’s recent metal tariffs. Following President Donald Trump’s early-March announcement that he would tax overseas metals — citing national security concerns with China as a rationale — the government imposed a 25 percent tax on steel and a 10 percent tax on aluminum imported from certain countries.
Since the initial announcement, steel prices have reportedly risen as much as 10 percent nationwide. Those increases could impact what developers pay for steel used to frame buildings, rebar that goes into reinforced concrete structures, studs for interior framings and aluminum casements for curtain walls, among other construction materials. “We can ill afford additional costs in the construction industry,” said Plaza Construction Group CEO Richard Wood.
Indeed, the Big Apple is already the most expensive place to build in the world, with costs averaging almost $3,807 per square meter, according to the consultancy and management firm Turner & Townsend. And construction costs — including materials and labor — rose nearly 4.5 percent in New York City in March from a year earlier, according to figures from national construction news magazine Engineering News-Record. Since 2012, costs are up a little more than 26 percent. “It’s certainly scary,” said David Schwartz of Slate Property Group, an active residential developer in the city.
“We’re definitely going to see increases in prices, but as for the total impact, we don’t quite know yet.” Despite the uncertainty, developers are already baking in the potential extra costs to their plans. Broadway Construction Group COO Joseph Aiello, for instance, is expecting up to a $400,000 increase in material costs due to the tariffs at the redevelopment of the Dime Savings Bank in Williamsburg.
The project’s developers, Tavros Capital Partners and Charney Construction & Development, are converting the property into a 23-story rental tower. “It’s something that I think people already are beginning to either hit the panic button on or just reacting to,” Aiello said.
There is a slew of other major development projects on the horizon that will need massive amounts of steel, including Silverstein Properties’ 2.8 million-square-foot 2 World Trade Center and Tishman Speyer’s 2.85 million-square-foot Spiral office tower in Hudson Yards. As of late last year, Tishman was in the market for a $1.5 billion construction loan for the project, though industry experts said it’s unlikely that lenders would be willing to increase financing packages to cover additional steel costs.
However, Steven Polivy, chair of the economic development and incentives practice at the law firm Akerman, said a company like Tishman can most likely source lower-priced steel. “I suspect they have made sure their steel suppliers are going to supply them with steel that is not subject to the tariff,” he said. “They have the bargaining power to make sure that they’re buying from domestic suppliers.”
Developers will also find other ways to ensure they’re not on the hook for the extra taxes, according to Polivy. More than likely, developers will try to purchase steel on a fixed-price basis, meaning that the supplier would be the responsible party if the product is subject to the tariffs. But even that isn’t a surefire safeguard. Polivy said he had a conversation last month with one developer who had already purchased his steel at a fixed price for a project in the city. The steel, it turned out, was coming from Canada and therefore was exempt from the tariff. But the developer was concerned about whether he or his supplier would be on the hook for any potential increases.
“The supplier would not have been able to afford to deliver the steel at the contract price if his cost went up 25 percent, so he would have defaulted under his contract,” Polivy said. Though the developer would have been able to sue, “he still would have a hole in the ground that he was paying taxes and insurance and contractor fees on.” It should be noted that 60 percent of the steel imported to the country comes from Canada and Mexico, which received waivers from the new tariffs. And Trump in late March announced he would temporarily suspend tariffs for Argentina, Australia, Brazil, South Korea, Canada, Mexico and the U.S.’s biggest trading partner — the European Union — until May 1, 2018.
There are many who feel any increases will be minimal, and certainly not as high as 25 percent. The tariffs also reportedly only apply to raw steel, as opposed to fabricated steel products. That, industry insiders say, presents a big loophole. Manufacturers in exempt countries like Canada and Mexico can import cheap Chinese steel, fabricate it into products and then ship it into the U.S., thereby avoiding the tariff. “I don’t see any impact on our industry in the short term,” said Kenneth Colao, president of the contractor CNY Group. The long-term effect on the marketplace, he added, will have more to do with whether there is “going to be more activity, more volume in the future.”
Others say there are issues, like a shortage of skilled labor, that would have a greater impact on commercial construction. That, coupled with any increases in costs for materials, “could cause development activity to slow unless rent growth is sufficient to offset higher costs,” said Spencer Levy, CBRE’s senior economic advisor and head of research for the Americas.
Still, one of the big remaining questions is how much of the additional cost homebuyers, apartment renters and office tenants will be willing to pay. Concessions in the office market are at an all-time high, partly due to record construction costs. When projects built with higher-cost metals hit the market two or three years down the line, however, residential buyers and renters may be more willing to absorb the extra costs.
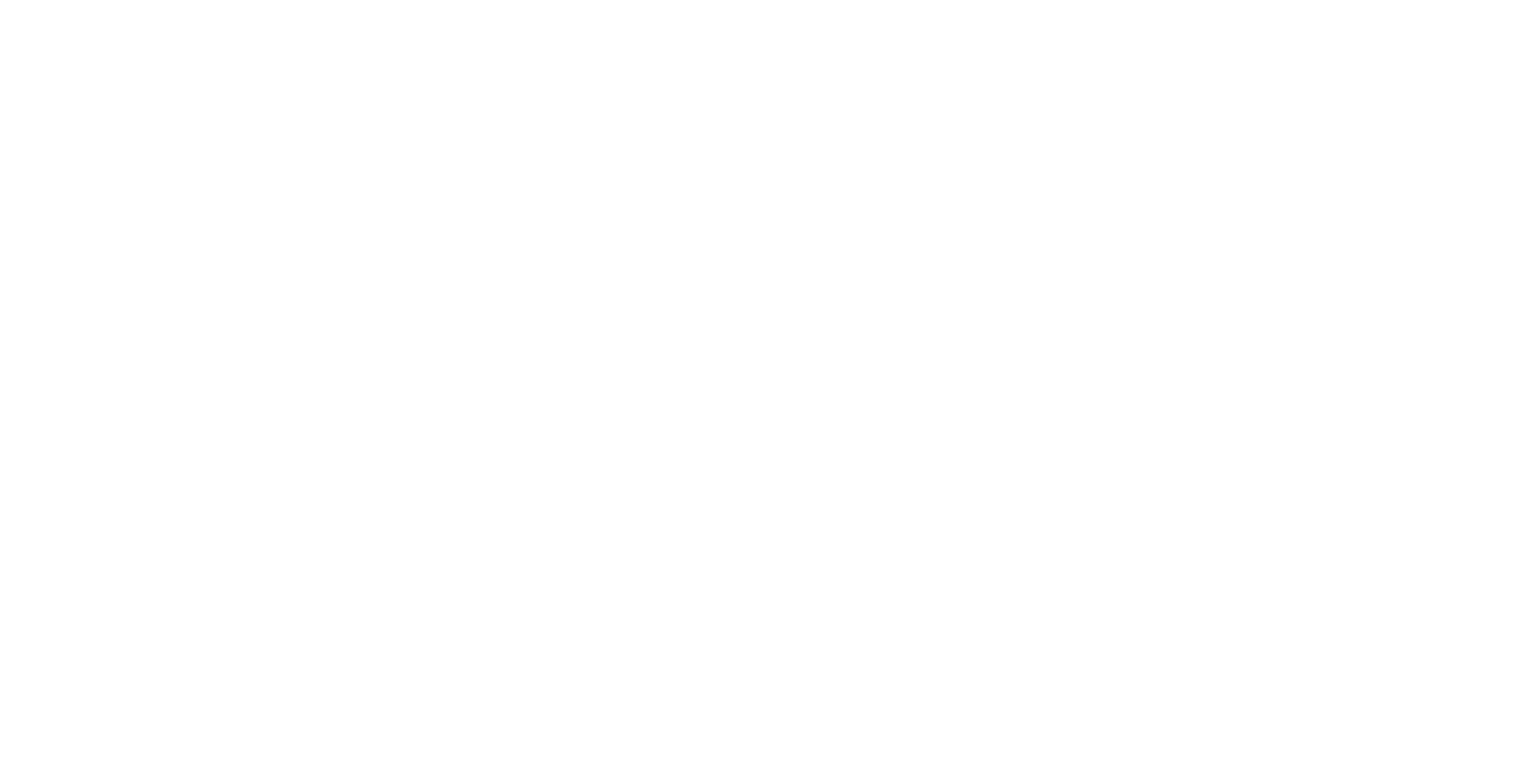
As a developer, “you can let [your subcontractor] default and walk away, but you’re not going to go out and get the job done any cheaper,” he explained.
“So it’s more advised to make peace with your subcontractor and help him, whether it’s by fronting him some money so that he can bring in materials earlier, or maybe splitting the increase with him.” Slate’s Schwartz said he was looking into the possibility of doing wood construction as an alternative. “It was something I never looked at, but I figured, hey, why not get knowledgeable?” he said, though he acknowledged that if there was a broader shift in the industry toward wood materials, their prices would increase as a result.
Daren Hornig, managing partner of Hornig Capital Partners, said he thinks increased costs on building materials will make project margins thinner.
But he said he’s more concerned with how a potential trade war could impact the overall economy and thus demand for real estate. And as of late last month, China requested that the U.S. provide compensation due to lost trade from the taxes and threatened to impose its own tariffs on $3 billion of U.S. imports including agricultural, steel and aluminum goods. “That could really throw things off from an overall economy standpoint and increase costs on [many construction and consumer products],” he said. “I’m more concerned how that’s going to play out.”
Share